Moisture Mitigation Strategies for Warehouses and Distribution Centers
The Hidden Threat Beneath Your Floors
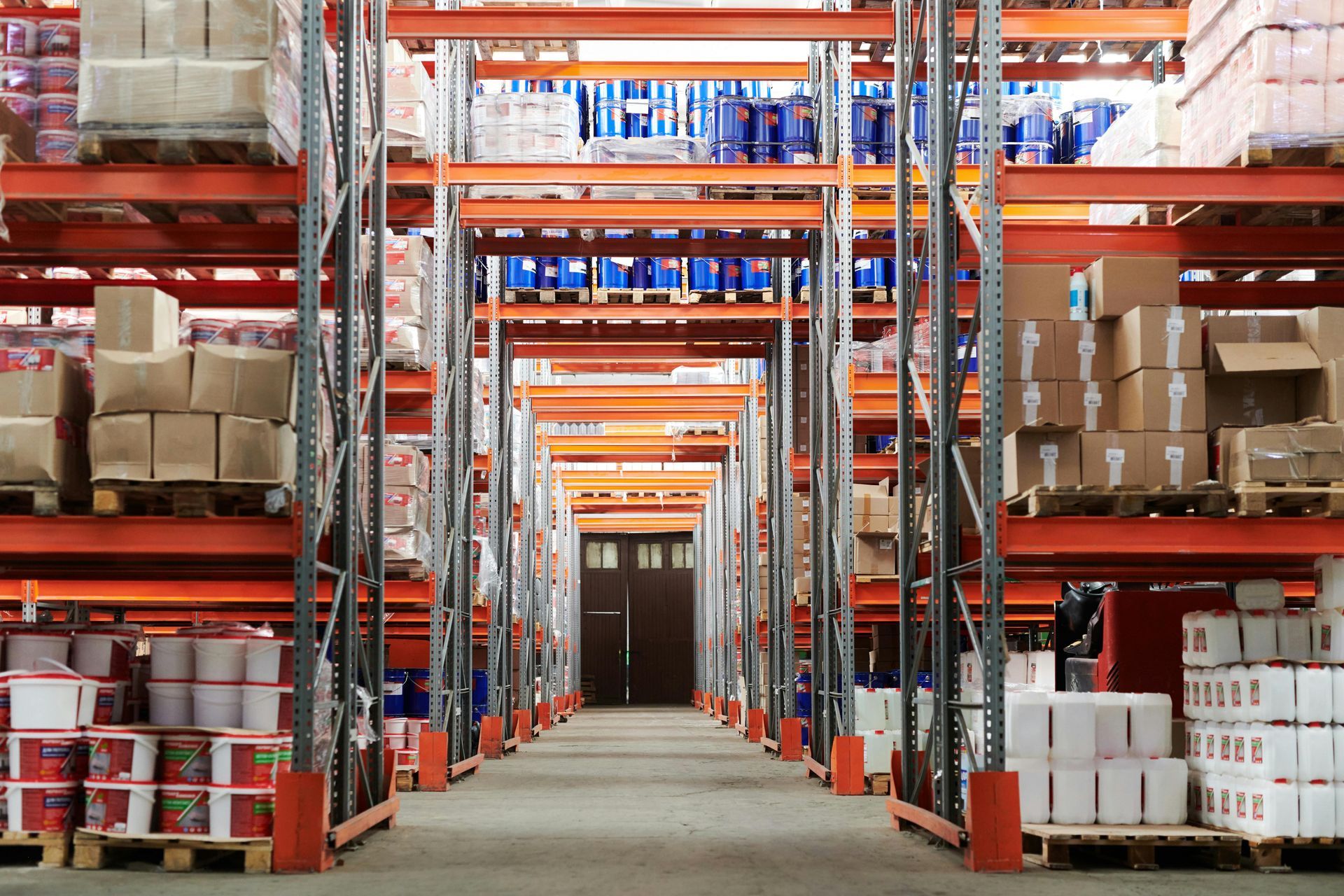
Warehouses and distribution centers are the lifeblood of logistics—busy, high-traffic spaces where productivity depends on seamless operations. But beneath the heavy shelving, forklifts, and miles of concrete lies a silent threat: moisture vapor. Many facilities managers don't realize that even a seemingly dry slab can harbor vapor pressure that leads to coating failure, delamination, discoloration, and downtime. The cost? Thousands in lost inventory, repairs, and production time.
At ACP, we’ve seen firsthand how moisture mitigation is the most overlooked—but most critical—step in flooring success. Too often, projects focus on polishing or sealing the surface, without addressing what lies beneath. Without a smart moisture strategy, everything is at risk. It’s not just a step—it’s the key to a successful installation. Let’s explore how a smart strategy below the surface can protect your concrete floors.
What Is Moisture Vapor Transmission (MVT)?
Concrete is porous. Water vapor naturally travels from the sub-slab toward the surface. In a warehouse environment with temperature fluctuations, this vapor can accumulate and force its way through coatings, adhesives, and finishes, wreaking havoc. Even newly poured slabs aren’t safe—concrete can take months to fully dry, and improper moisture testing is a recipe for disaster.
Symptoms of a Moisture Problem
- Blistering or bubbling coatings
- Peeling paint or adhesives
- Damp or discolored floors
- White powdery residue (efflorescence)
- Mold growth at the base of shelving or walls
If you’ve seen any of these in your warehouse, you’re likely dealing with MVT.
The ACP Mitigation System
We don’t just coat over problems—we solve them. Our moisture mitigation approach is rooted in diagnostic testing, system design, and long-term performance.
Step 1: Thorough Moisture Evaluation
We begin with a comprehensive assessment of the concrete slab to identify any moisture concerns. This includes checking for signs of vapor emissions, trapped moisture, or other underlying issues that could affect floor performance.
We use for testing:
- Relative Humidity (RH) Probes drilled into the slab
- Calcium Chloride testing for surface emissions
- Moisture meters and thermal imaging for visual diagnostics
A clear understanding of the slab’s condition allows us to make informed decisions about the best path forward.
Step 2: Tailored Mitigation Strategy
Based on the evaluation, we apply a customized moisture mitigation system designed to block vapor and protect the integrity of the floor. Solutions may include barriers, hardeners, or leveling compounds that work together to create a durable, moisture-resistant foundation—ensuring long-term performance of any surface installed above.
Step 3: Floor Coating Integration
Once the moisture barrier is secure, we apply ACP’s high-performance coatings—tailored for the warehouse’s operational demands. Whether it’s heavy forklift traffic, pallet scuffing, or chemical spills, our coating systems stand up to the stress.
Why It Matters: Avoiding Costly Failures
Moisture-related flooring failures cost U.S. businesses over $1 billion annually. But with proper mitigation, you can:
- Extend the lifespan of coatings and adhesives
- Maintain warranty compliance on finishes and materials
- Prevent downtime from repairs and recoating
- Avoid insurance claims due to mold, mildew, or slip hazards
Bonus: Sustainable & Smart Solutions
Our moisture mitigation strategies also support:
- LEED Credits for indoor environmental quality
- Low-VOC applications for better air quality
- Energy savings by preserving insulation value of the floor system
Moisture may be invisible, but the damage it causes is not. With ACP’s proactive moisture mitigation services, your warehouse floor will remain a solid foundation—not a ticking time bomb. If you’re investing in coatings, ensure you protect that investment from the ground up.
Contact ACP today to learn how we can keep your operation dry, durable, and dependable.
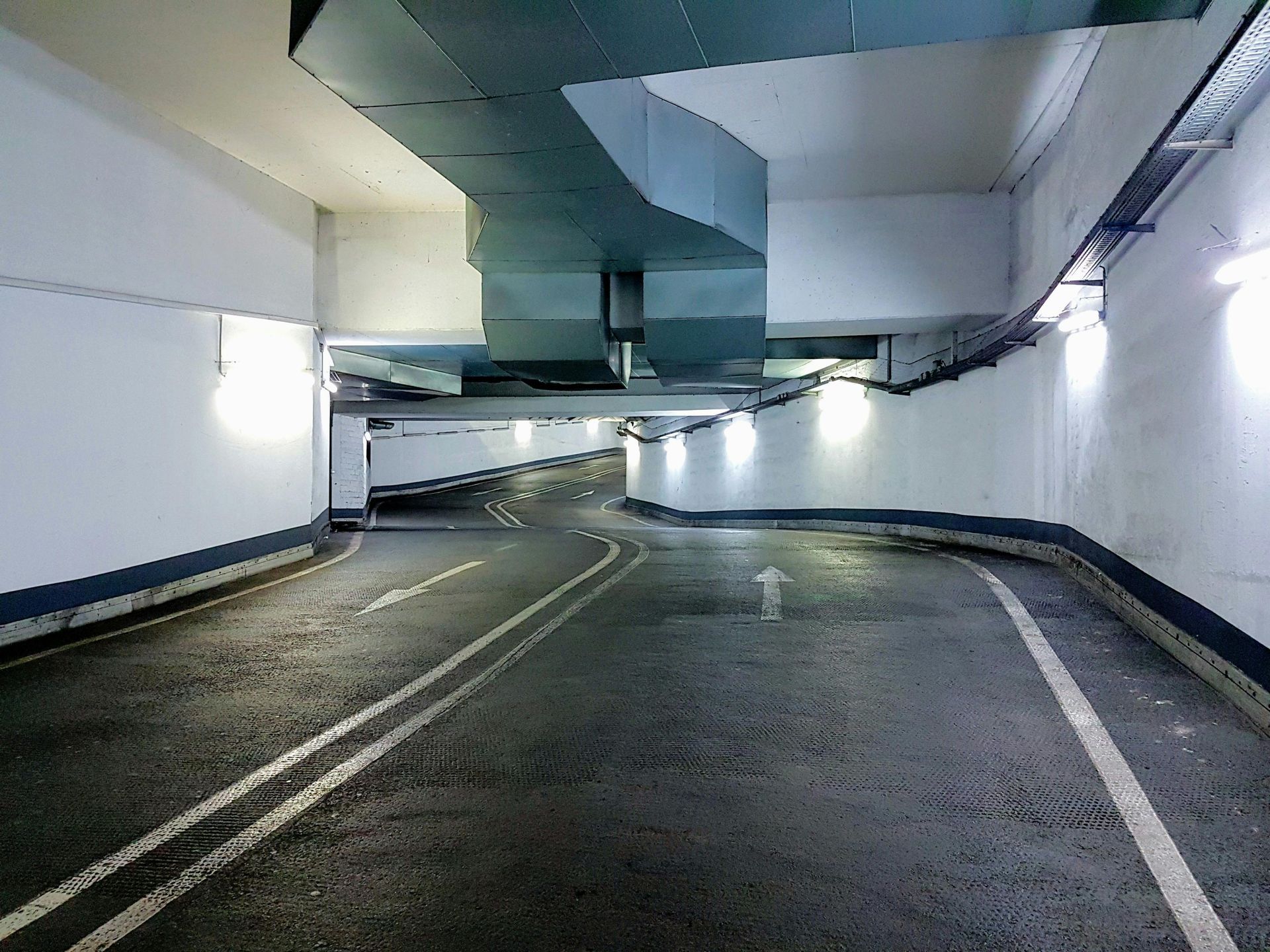
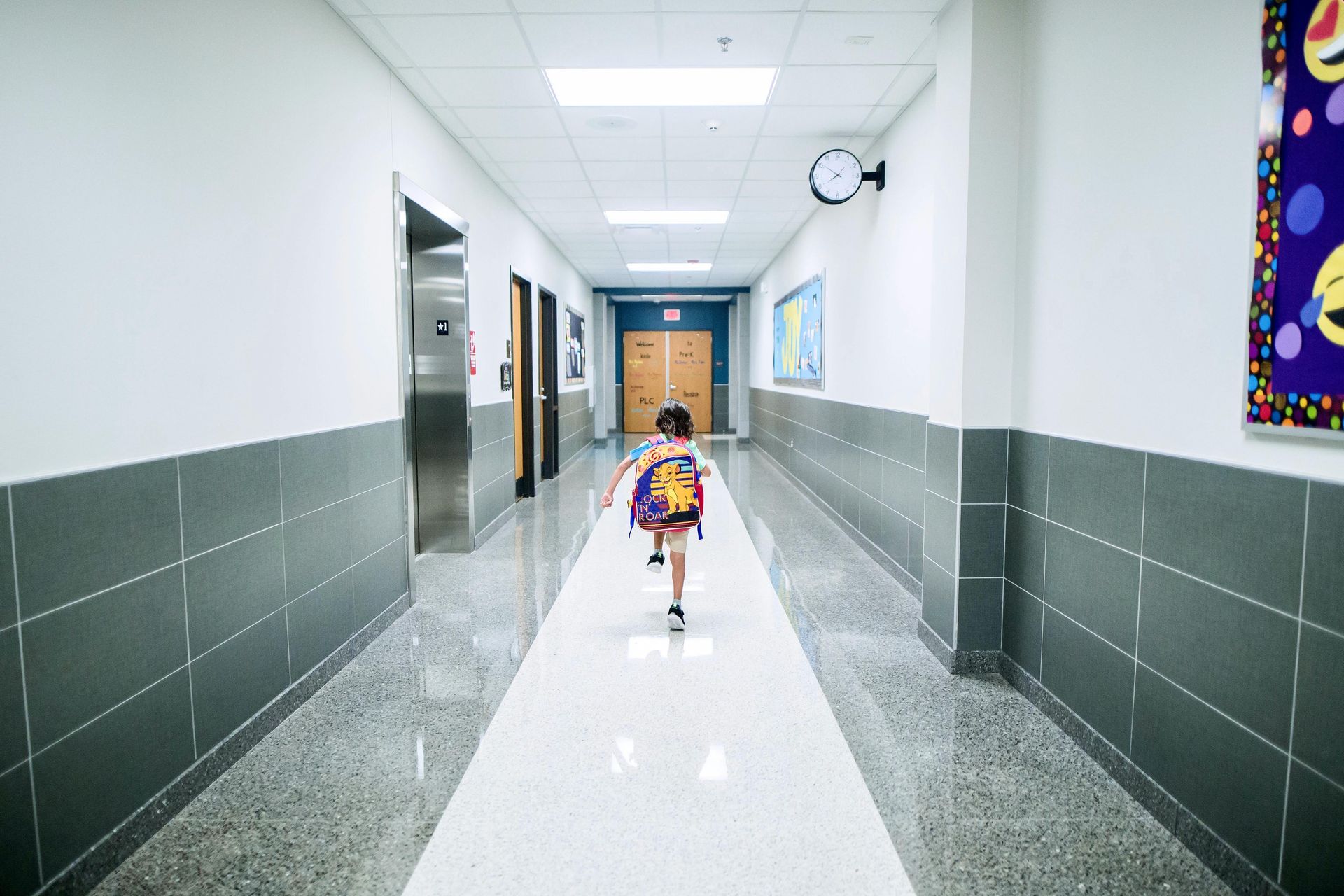