Ensuring Compliance with OSHA’s Updated Walking-Working Surfaces Standard: How ACP’s Services Keep Workplaces Safe
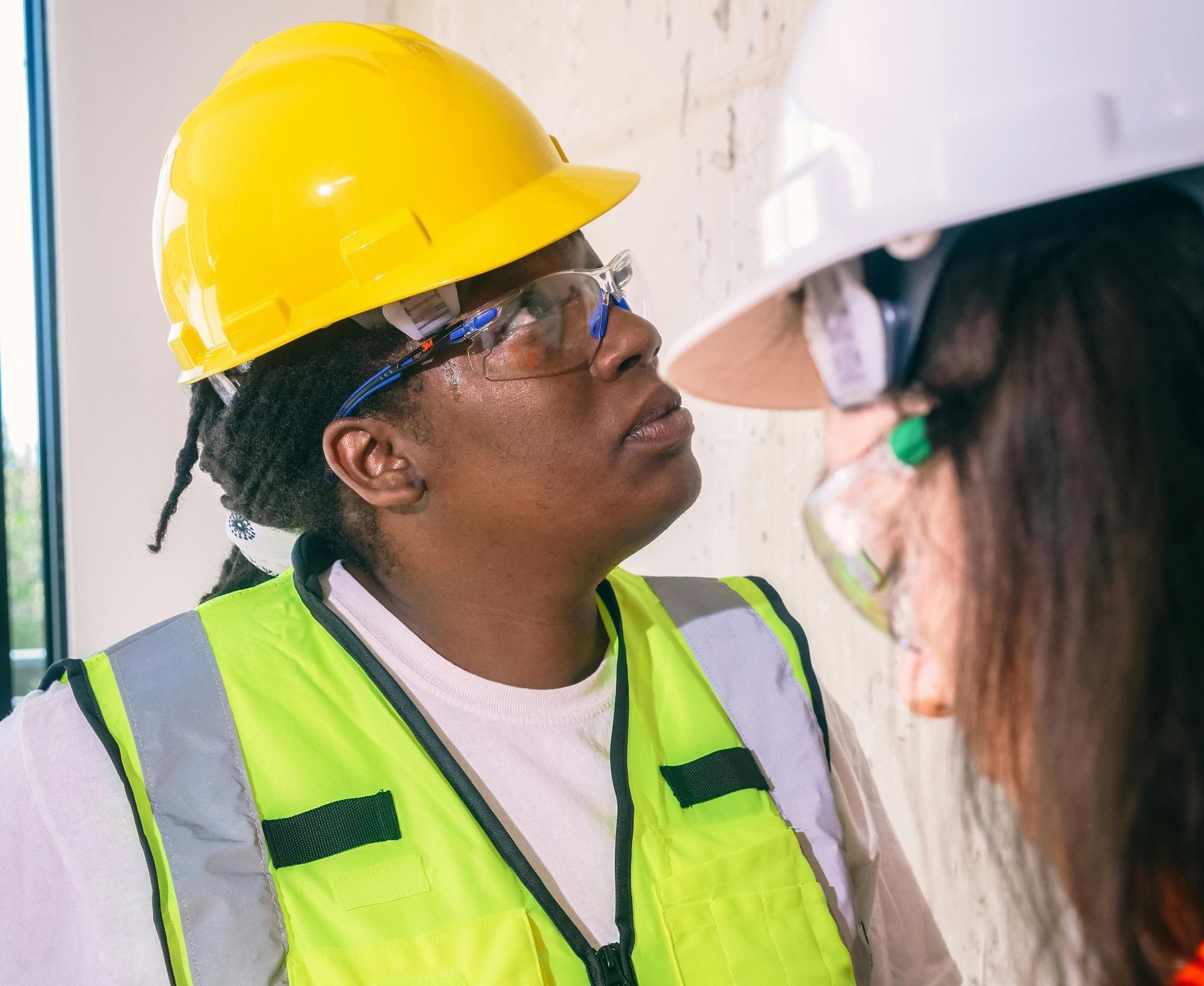
Workplace safety is non-negotiable, especially when it comes to preventing slips, trips, and falls—one of the leading causes of workplace injuries. In response to these risks, the Occupational Safety and Health Administration (OSHA) has updated its Walking-Working Surfaces and Personal Fall Protection Systems standard (29 CFR Part 1910, Subparts D and I), requiring employers to inspect, maintain, and improve walking surfaces to prevent hazards.
For industrial, manufacturing, and commercial facilities, these regulatory updates can mean costly compliance requirements—unless you have the right flooring solutions in place. ACP’s durable, slip-resistant flooring and protective coatings provide long-lasting compliance with OSHA’s latest standards while enhancing workplace safety and efficiency.
Understanding OSHA’s Updated Regulations
OSHA’s updated standard applies to all general industry workplaces and covers all walking-working surfaces, such as floors, ladders, stairways, and platforms. The most relevant updates include:
- Regular Inspections – Employers must conduct routine inspections of all walking-working surfaces to identify and correct hazards before they lead to injuries. (ecfr.gov)
- Housekeeping & Surface Maintenance – Floors must be kept clean, dry, and free of hazards like spills, cracks, or debris to prevent slips. (osha.gov)
- Slip, Trip, and Fall Prevention – Employers must use high-traction flooring, coatings, and protective systems to reduce fall risks.
Failure to comply with these standards can result in significant fines, legal consequences, and increased liability risks.
How ACP’s Services Help Companies Stay OSHA Compliant
ACP specializes in flooring solutions that address OSHA’s latest requirements, preventing hazards and ensuring compliance across industries.
1. Slip-Resistant Coatings for Walking-Working Surfaces
One of OSHA’s top requirements is ensuring walking surfaces are slip-resistant to prevent falls. ACP’s high-performance polyurea and epoxy coatings create a textured, non-slip finish that significantly reduces accident risks—even in wet or greasy environments. According to industry benchmarks, commercial flooring should achieve a Dynamic Coefficient of Friction (DCOF) ≥ 0.42, as outlined in ANSI A326.3, to be considered safe when wet. ACP’s coatings meet or exceed this standard, helping your facility stay compliant and safe.
✅ Ideal for: Warehouses, manufacturing plants, food processing facilities, and distribution centers.
✅ Meets OSHA Compliance: Provides high-traction, durable surfaces that remain slip-resistant even in wet or high-traffic conditions.
2. Concrete Resurfacing & Repair to Eliminate Hazards
Cracked, uneven, or deteriorated flooring is a major OSHA violation and a leading cause of workplace injuries. ACP’s concrete resurfacing and restoration services eliminate these risks by:
- Smoothing uneven surfaces to prevent trips and falls.
- Repairing cracks and damage that compromise safety.
- Enhancing durability to withstand heavy traffic and machinery use.
✅ Ideal for: Industrial warehouses, parking structures, and logistics facilities.
✅ Meets OSHA Compliance: Keeps floors level, durable, and hazard-free, meeting OSHA’s housekeeping and maintenance standards.
3. Moisture Mitigation to Prevent Slippery Surfaces
OSHA’s regulations require employers to maintain dry, non-slippery flooring. Excessive moisture buildup from spills, humidity, or condensation can lead to dangerous slip hazards. ACP’s moisture mitigation solutions prevent these issues by:
- Applying waterproof coatings that prevent water absorption.
- Installing drainage solutions to keep surfaces dry and safe.
- Reducing condensation buildup on concrete and coated surfaces.
✅ Ideal for: Food processing plants, healthcare facilities, and industrial kitchens.
✅ Meets OSHA Compliance: Maintains dry, slip-resistant surfaces to prevent injuries.
4. Secondary Containment Systems for Spill Prevention
In industries handling hazardous liquids, OSHA requires proper containment measures to prevent spills from creating hazardous walking conditions. ACP’s polyurea containment coatings provide seamless, waterproof protection for secondary containment areas.
- Prevents chemical and liquid spills from spreading.
- Creates a waterproof barrier that protects floors and containment zones.
- Fast-curing application minimizes downtime.
✅ Ideal for: Oil & gas, chemical plants, and industrial storage facilities.
✅ Meets OSHA Compliance: Ensures containment areas meet spill-prevention requirements, reducing risks of exposure and slip hazards.
The Cost of Non-Compliance vs. The Value of Prevention
Failing to comply with OSHA’s updated standards can result in:
- Fines & Penalties: OSHA citations for unsafe walking surfaces can range from $15,000 to $150,000+ per violation.
- Increased Liability: Workplace injuries lead to higher insurance costs, lawsuits, and lost productivity.
- Operational Disruptions: Unsafe conditions can force temporary shutdowns, affecting profits and business continuity.
By investing in ACP’s slip-resistant flooring, resurfacing, and containment solutions, companies avoid costly fines while creating a safer, more efficient workplace.
Stay Compliant, Stay Safe
OSHA’s updated walking-working surfaces standard means businesses must take proactive steps to prevent slips, trips, and falls. ACP’s flooring and containment solutions offer a cost-effective, long-term approach to OSHA compliance, reducing risk and improving workplace safety. Don’t wait until an inspection or workplace incident forces costly changes—take action now.
Contact ACP today for a free consultation on how to upgrade your facility’s flooring to meet OSHA’s latest safety requirements!
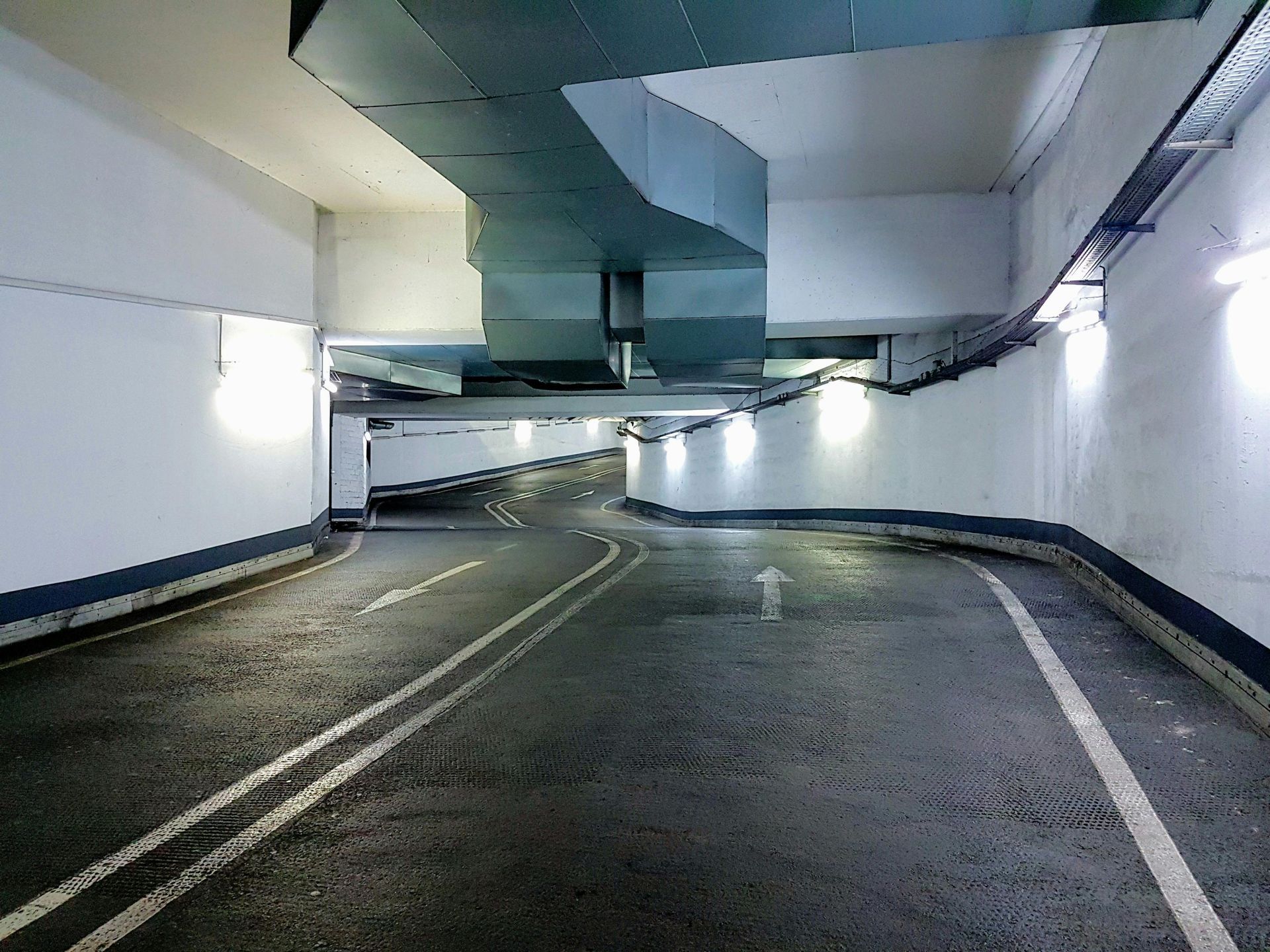